top of page
Standard Products
Explore Materials & Manufacturing Methods

HYDRAULIC COMPRESSION MOULDED PARTS
PRODUCT DESCRIPTION:
As the traditional metal parts are now being produced from polymers, hydraulic compression moulding has become one of the fastest-growing sectors in hydraulic systems. In the Hydraulic Compression Moulding process, the moulding material in granular or powder form is mostly preheated and is compressed under pressure, using two moulds. The heat and pressure are maintained throughout the process, until the material has cured, aiding the production of the desired shapes. This method is followed for making products by using PTFE, filled PTFE compounds and PEEK.
This moulding process is a great option for comparatively simple designs, including large basic shapes which are not possible to produce by using the extrusion process.
ADVANTAGES:
- Cost-Efficient
The Hydraulic Compression moulding is often the most economical manufacturing method, with lower tooling cost.
- Good for large parts production
This form of moulding process is suitable for manufacturing large parts that are mostly flat, simple, and thick, that involves the use of significant bulk of material to produce.
- High durability
With this moulding process the parts that are manufactured are free of flow marks and knit lines. Due to high structural stability of compression moulded parts, the parts can be produced with high durability.
- Design Flexibility
The Hydraulic compression moulding does not require to account for the tooling features such as gates, sprues or runners, which are used in other production methods. This aids the engineers to design the products with greater flexibility.
APPLICATIONS:
Hydraulic Compression moulding has numerous applications. The products that are compression molded are listed below:
- Automobile parts: Various plastic parts that are used in engine components such as valve seats and valve plugs, bearings, piston rings and seals
- Electrical components: Electrical wall receptacles, sockets, meter cases, switches, faceplates, and circuit breakers.
- Valve Industries: Valve seats, spherical balls, V-rings.
As the traditional metal parts are now being produced from polymers, hydraulic compression moulding has become one of the fastest-growing sectors in hydraulic systems. In the Hydraulic Compression Moulding process, the moulding material in granular or powder form is mostly preheated and is compressed under pressure, using two moulds. The heat and pressure are maintained throughout the process, until the material has cured, aiding the production of the desired shapes. This method is followed for making products by using PTFE, filled PTFE compounds and PEEK.
This moulding process is a great option for comparatively simple designs, including large basic shapes which are not possible to produce by using the extrusion process.
ADVANTAGES:
- Cost-Efficient
The Hydraulic Compression moulding is often the most economical manufacturing method, with lower tooling cost.
- Good for large parts production
This form of moulding process is suitable for manufacturing large parts that are mostly flat, simple, and thick, that involves the use of significant bulk of material to produce.
- High durability
With this moulding process the parts that are manufactured are free of flow marks and knit lines. Due to high structural stability of compression moulded parts, the parts can be produced with high durability.
- Design Flexibility
The Hydraulic compression moulding does not require to account for the tooling features such as gates, sprues or runners, which are used in other production methods. This aids the engineers to design the products with greater flexibility.
APPLICATIONS:
Hydraulic Compression moulding has numerous applications. The products that are compression molded are listed below:
- Automobile parts: Various plastic parts that are used in engine components such as valve seats and valve plugs, bearings, piston rings and seals
- Electrical components: Electrical wall receptacles, sockets, meter cases, switches, faceplates, and circuit breakers.
- Valve Industries: Valve seats, spherical balls, V-rings.

ISOSTATIC MOULDED PARTS
PRODUCT DESCRIPTION:
Isostatic moulding is a manufacturing method where the pressure is evenly applied in all directions on the moulding material in granular form throughout the cycle time, which is suitable to produce complex part shapes in a broad size range having uniform physical properties This method differs from Compression moulding which applies pressure only in a single direction. In contrast to the compression moulded and extruded parts, materials that are isostatically moulded have better consistent material properties.
The product shapes that are produced from the Isostatic moulding process, are close to the geometries of the required finished products. This manufacturing method is suitable for repetitive batch manufacturing of PTFE, filled PTFE grades, and PEEK. Vimal Polymers can produce complex and large shapes part with high quality
ADVANTAGES:
- Cost-Effective
Isostatic moulding is a cost-effective manufacturing method, as the parts obtained are near net shapes. Hence, less material is used as compared to the standard use of cylinders or blocks
- Good material properties
As the material is compressed under vacuum, the parts are virtually free of porosity, aiding in better material characteristics by improving mechanical and dielectric properties
- Better corrosion resistance
- Both Thin and thick walls can be manufactured
- High Thermal resistance
- FDA compliant
- Repeatability
- More intricate shapes can be produced
APPLICATIONS:
- Common shapes such as Tapered sleeves and closed-end cylinders are isostatically moulded
- Houseware: One-piece turner, Cups and buckets
- Valve & Corrosion Industry: Pipe & column liners, Valve liners (diaphragm), Pipe fittings such as tees, elbows & reducers, Nozzles, Bellows, Pump liners (centrifugal, screw), Impellers, agitators and mixer paddles
- Electrical Industry: High voltage insulators
- Medical & Chemical Industries: Pressure vessels, tanks & containers
Isostatic moulding is a manufacturing method where the pressure is evenly applied in all directions on the moulding material in granular form throughout the cycle time, which is suitable to produce complex part shapes in a broad size range having uniform physical properties This method differs from Compression moulding which applies pressure only in a single direction. In contrast to the compression moulded and extruded parts, materials that are isostatically moulded have better consistent material properties.
The product shapes that are produced from the Isostatic moulding process, are close to the geometries of the required finished products. This manufacturing method is suitable for repetitive batch manufacturing of PTFE, filled PTFE grades, and PEEK. Vimal Polymers can produce complex and large shapes part with high quality
ADVANTAGES:
- Cost-Effective
Isostatic moulding is a cost-effective manufacturing method, as the parts obtained are near net shapes. Hence, less material is used as compared to the standard use of cylinders or blocks
- Good material properties
As the material is compressed under vacuum, the parts are virtually free of porosity, aiding in better material characteristics by improving mechanical and dielectric properties
- Better corrosion resistance
- Both Thin and thick walls can be manufactured
- High Thermal resistance
- FDA compliant
- Repeatability
- More intricate shapes can be produced
APPLICATIONS:
- Common shapes such as Tapered sleeves and closed-end cylinders are isostatically moulded
- Houseware: One-piece turner, Cups and buckets
- Valve & Corrosion Industry: Pipe & column liners, Valve liners (diaphragm), Pipe fittings such as tees, elbows & reducers, Nozzles, Bellows, Pump liners (centrifugal, screw), Impellers, agitators and mixer paddles
- Electrical Industry: High voltage insulators
- Medical & Chemical Industries: Pressure vessels, tanks & containers

RAM EXTRUDED PRODUCTS
PRODUCT DESCRIPTION:
Ram extrusion is the process where, a ram or plunger is used which forces the material through a die at the end, instead of an extrusion screw. As the screw extruder has high viscoelasticity for PTFE and other polymers after heating, it is not recommended to use it. Hence, it is required to use a ram extruder. Here the PTFE or PEEK material is fed into a chamber, where it is pushed by a ram and continuously heated through an extrusion tube of the die. The preforming, sintering, and cooling processes then occur consecutively inside the die. The die provides mostly round-shaped objects such as tubes, rods, and profiles, etc.
ADVANTAGES:
- Ram extrusion is a continuous process that can produce products with lengths of up to 6 meters
- Complex shapes can be produced with a consistent cross-section
- High production volumes
- More affordable
- Good for producing round-shaped products
- Short setting up time for die change
APPLICATIONS:
- Ram extrusion process is typically used for manufacturing profiles, tubing, rods, sleeves, etc.
- PTFE Pipe: For handling strong chemicals (Petroleum products, aircraft industry, automobile industry, Pharmaceuticals)
- PTFE Rods: For insulation of electrical equipment
Ram extrusion is the process where, a ram or plunger is used which forces the material through a die at the end, instead of an extrusion screw. As the screw extruder has high viscoelasticity for PTFE and other polymers after heating, it is not recommended to use it. Hence, it is required to use a ram extruder. Here the PTFE or PEEK material is fed into a chamber, where it is pushed by a ram and continuously heated through an extrusion tube of the die. The preforming, sintering, and cooling processes then occur consecutively inside the die. The die provides mostly round-shaped objects such as tubes, rods, and profiles, etc.
ADVANTAGES:
- Ram extrusion is a continuous process that can produce products with lengths of up to 6 meters
- Complex shapes can be produced with a consistent cross-section
- High production volumes
- More affordable
- Good for producing round-shaped products
- Short setting up time for die change
APPLICATIONS:
- Ram extrusion process is typically used for manufacturing profiles, tubing, rods, sleeves, etc.
- PTFE Pipe: For handling strong chemicals (Petroleum products, aircraft industry, automobile industry, Pharmaceuticals)
- PTFE Rods: For insulation of electrical equipment

PASTE EXTRUDED PRODUCTS
PRODUCT DESCRIPTION:
Products manufactured by Paste extrusion technology enables Vimal Polymers to broaden the PTFE product line with additional designs and profiles. In this manufacturing method, very close process control of the PTFE grain size range is maintained. For the paste extrusion process, the extrudable PTFE fine powders are blended with a volatile lubricant (hydrocarbon) for preparing the paste, which is then pre-pressed and filled in a PTFE paste extruder. The preform paste is compressed in a cold or in the preheated stage through a die. The part obtained is separated from the lubricant, followed by the sintering process.
For the paste extrusion process, the production is done in batch quantities. We can manufacture the paste extruded products according to the applications with required chemical, physical and mechanical properties.
ADVANTAGES:
- Good surface finish
- Close dimensional control
- Highly flexible structure
- Lower void content between PTFE particles
- High toughness
- Less space between particles
- Resistance to permeation
- Cost-effective
APPLICATIONS:
- PTFE pipe liners: For transfer hoses, pipe fittings
- PTFE rods: For gaskets, seals, and lubricating materials (Chemical and - Pharmaceutical Industries) and insulating electrical components (Electrical Industry)
- PTFE tapes: For leaks, gas pipe sealing, and sealing of fuel line joints (Automotive Industry)
- PTFE tubes
Products manufactured by Paste extrusion technology enables Vimal Polymers to broaden the PTFE product line with additional designs and profiles. In this manufacturing method, very close process control of the PTFE grain size range is maintained. For the paste extrusion process, the extrudable PTFE fine powders are blended with a volatile lubricant (hydrocarbon) for preparing the paste, which is then pre-pressed and filled in a PTFE paste extruder. The preform paste is compressed in a cold or in the preheated stage through a die. The part obtained is separated from the lubricant, followed by the sintering process.
For the paste extrusion process, the production is done in batch quantities. We can manufacture the paste extruded products according to the applications with required chemical, physical and mechanical properties.
ADVANTAGES:
- Good surface finish
- Close dimensional control
- Highly flexible structure
- Lower void content between PTFE particles
- High toughness
- Less space between particles
- Resistance to permeation
- Cost-effective
APPLICATIONS:
- PTFE pipe liners: For transfer hoses, pipe fittings
- PTFE rods: For gaskets, seals, and lubricating materials (Chemical and - Pharmaceutical Industries) and insulating electrical components (Electrical Industry)
- PTFE tapes: For leaks, gas pipe sealing, and sealing of fuel line joints (Automotive Industry)
- PTFE tubes

AUTOMATIC MOULDED PARTS
PRODUCT DESCRIPTION:
PTFE products can be manufactured by using manual, semi-automatic or automatic moulding machines. The automatic compression moulding method is superior to others, as it is more efficient and more intelligent. In this process, the moulding material in granular or powder form is mostly preheated and is compressed under pressure, using two moulds. The heat and pressure are maintained throughout the process, until the material has cured, aiding the production of the desired shapes. However, the complete compression moulding process is controlled by an intelligent PLC controlling system, where the parameters like pressure, speed, range, dwell time, and quantity can be set as per the requirement. This makes the whole manufacturing process simple and efficient. By using the Automatic moulding process, the possibility of producing complex shapes is increased and the products obtained are of premium quality, with excellent surface finish.
ADVANTAGES:
- Automatic moulding process ensures efficient production
- Complex bends and intricate shapes can be produced
- Moulded products have better properties, such as density, tensile strength, etc.
- Less raw material required
- High production volumes
- Low energy & tool maintenance costs
APPLICATIONS:
- Automatic moulding has numerous applications and is used for the production of the parts listed below:
- Automobile parts: Various plastic parts that are used in engine components such as valve seats and valve plugs, bearings, piston rings, seals along with vehicle interior can be compression molded, too.
- Electrical components: Electrical wall receptacles, sockets, meter cases, switches, faceplates, and circuit breakers.
- Valve Industries: Valve seats, spherical balls, V-rings.
PTFE products can be manufactured by using manual, semi-automatic or automatic moulding machines. The automatic compression moulding method is superior to others, as it is more efficient and more intelligent. In this process, the moulding material in granular or powder form is mostly preheated and is compressed under pressure, using two moulds. The heat and pressure are maintained throughout the process, until the material has cured, aiding the production of the desired shapes. However, the complete compression moulding process is controlled by an intelligent PLC controlling system, where the parameters like pressure, speed, range, dwell time, and quantity can be set as per the requirement. This makes the whole manufacturing process simple and efficient. By using the Automatic moulding process, the possibility of producing complex shapes is increased and the products obtained are of premium quality, with excellent surface finish.
ADVANTAGES:
- Automatic moulding process ensures efficient production
- Complex bends and intricate shapes can be produced
- Moulded products have better properties, such as density, tensile strength, etc.
- Less raw material required
- High production volumes
- Low energy & tool maintenance costs
APPLICATIONS:
- Automatic moulding has numerous applications and is used for the production of the parts listed below:
- Automobile parts: Various plastic parts that are used in engine components such as valve seats and valve plugs, bearings, piston rings, seals along with vehicle interior can be compression molded, too.
- Electrical components: Electrical wall receptacles, sockets, meter cases, switches, faceplates, and circuit breakers.
- Valve Industries: Valve seats, spherical balls, V-rings.

VIRGIN PTFE
PRODUCT DESCRIPTION:
Virgin PTFE grade material is created from pure resin of PTFE without adding any other material. It is one of the most inert materials, that is used in various industrial applications. Because of the chemical structure of the PTFE polymer, the fluorine atoms form a homogenous sheath around carbon atoms, thereby aiding the polymer with chemical resistance and stability. Virgin PTFE is mostly used for the components where temperature and chemical resistance is important instead of mechanical properties.
PROPERTIES:
- Excellent chemical resistance
- Excellent electrical insulation
- High flexibility
- High melting point
- High thermal stability
- Low coefficient of friction
- Flame-retardant properties
- Good non-stick properties
APPLICATIONS:
Virgin PTFE has a wide range of applications. They are:
- O-Rings
- Gaskets
- Bellows
- Valve seats
- Electrical connectors
- Pump housings
- Housings for filter
- Seals
- Chemical & Pharmaceutical Industry
- Fume purification
- Filtration technology
- Food and Medical Industry
Virgin PTFE grade material is created from pure resin of PTFE without adding any other material. It is one of the most inert materials, that is used in various industrial applications. Because of the chemical structure of the PTFE polymer, the fluorine atoms form a homogenous sheath around carbon atoms, thereby aiding the polymer with chemical resistance and stability. Virgin PTFE is mostly used for the components where temperature and chemical resistance is important instead of mechanical properties.
PROPERTIES:
- Excellent chemical resistance
- Excellent electrical insulation
- High flexibility
- High melting point
- High thermal stability
- Low coefficient of friction
- Flame-retardant properties
- Good non-stick properties
APPLICATIONS:
Virgin PTFE has a wide range of applications. They are:
- O-Rings
- Gaskets
- Bellows
- Valve seats
- Electrical connectors
- Pump housings
- Housings for filter
- Seals
- Chemical & Pharmaceutical Industry
- Fume purification
- Filtration technology
- Food and Medical Industry

GLASS FILLED PTFE
PRODUCT DESCRIPTION:
Glass fibres are used as the filler for reinforcing the Glass filled PTFE. Due to the addition of this filler the mechanical properties, such as creep performance, wear resistance, and compressive strength of the PTFE is improved. Glass filled PTFE are suitable for the environments of oxidizing nature. According to the application requirement, the filler percentage composition of glass fibre can be accommodated as per requirement. With the increase in glass fibre filler percentage, the mechanical properties of the PTFE also improve, but this also increases the coefficient of friction as compared to that of Virgin PTFE.
PROPERTIES:
- Excellent wear resistance
- Improved hardness
- High toughness
- Less thermal expansion
- Excellent electrical insulation
- High flexibility
- High melting point
- High thermal stability
- Higher coefficient of friction
- Flame-retardant properties
APPLICATIONS:
Glass filled PTFE has a wide range of applications. They are:
- Valve seats
- Roller coverings
- Gaskets
- Bellows
- Electrical connectors
- Pump housings
- Housings for filter
- Seals
- Chemical & Pharmaceutical Industry
- Filtration technology
- Food and Medical Industry
Glass fibres are used as the filler for reinforcing the Glass filled PTFE. Due to the addition of this filler the mechanical properties, such as creep performance, wear resistance, and compressive strength of the PTFE is improved. Glass filled PTFE are suitable for the environments of oxidizing nature. According to the application requirement, the filler percentage composition of glass fibre can be accommodated as per requirement. With the increase in glass fibre filler percentage, the mechanical properties of the PTFE also improve, but this also increases the coefficient of friction as compared to that of Virgin PTFE.
PROPERTIES:
- Excellent wear resistance
- Improved hardness
- High toughness
- Less thermal expansion
- Excellent electrical insulation
- High flexibility
- High melting point
- High thermal stability
- Higher coefficient of friction
- Flame-retardant properties
APPLICATIONS:
Glass filled PTFE has a wide range of applications. They are:
- Valve seats
- Roller coverings
- Gaskets
- Bellows
- Electrical connectors
- Pump housings
- Housings for filter
- Seals
- Chemical & Pharmaceutical Industry
- Filtration technology
- Food and Medical Industry

CARBON FILLED PTFE
PRODUCT DESCRIPTION:
Virgin PTFE has good wear resistance, elastic and frictional properties, but its mechanical strength cannot withstand dynamic and high-pressure applications. Hence, Carbon is added in PTFE in the form of powder or fibres as the filler material, which improves the mechanical properties such as compressive strength and wear resistance of the PTFE. This makes the Carbon filled PTFE an excellent choice of material for rings and seals in a dynamic and high-pressure environment. As carbon is a conductive material, this ensures the suitability of Carbon filled PTFE products for higher thermal applications.
PROPERTIES:
- Excellent compressive strength
- Good thermal conductivity
- Excellent wear resistance
- Excellent chemical resistance
- Low permeability
- Improved hardness
- High toughness
- High flexibility
- Low coefficient of friction
- Flame-retardant properties
- Excellent dielectric properties
APPLICATIONS:
Carbon filled PTFE has a wide range of applications. They are:
- Commonly used for dynamic sealing applications
- Piston rings
- Compressor rings
- Valve seats
- Gaskets
- Bellows
- Electrical connectors
- Pump housings
- Chemical & Pharmaceutical Industry
- Filtration technology
- Automotive Industry
- Food and Medical Industry
- Packaging industry
Virgin PTFE has good wear resistance, elastic and frictional properties, but its mechanical strength cannot withstand dynamic and high-pressure applications. Hence, Carbon is added in PTFE in the form of powder or fibres as the filler material, which improves the mechanical properties such as compressive strength and wear resistance of the PTFE. This makes the Carbon filled PTFE an excellent choice of material for rings and seals in a dynamic and high-pressure environment. As carbon is a conductive material, this ensures the suitability of Carbon filled PTFE products for higher thermal applications.
PROPERTIES:
- Excellent compressive strength
- Good thermal conductivity
- Excellent wear resistance
- Excellent chemical resistance
- Low permeability
- Improved hardness
- High toughness
- High flexibility
- Low coefficient of friction
- Flame-retardant properties
- Excellent dielectric properties
APPLICATIONS:
Carbon filled PTFE has a wide range of applications. They are:
- Commonly used for dynamic sealing applications
- Piston rings
- Compressor rings
- Valve seats
- Gaskets
- Bellows
- Electrical connectors
- Pump housings
- Chemical & Pharmaceutical Industry
- Filtration technology
- Automotive Industry
- Food and Medical Industry
- Packaging industry
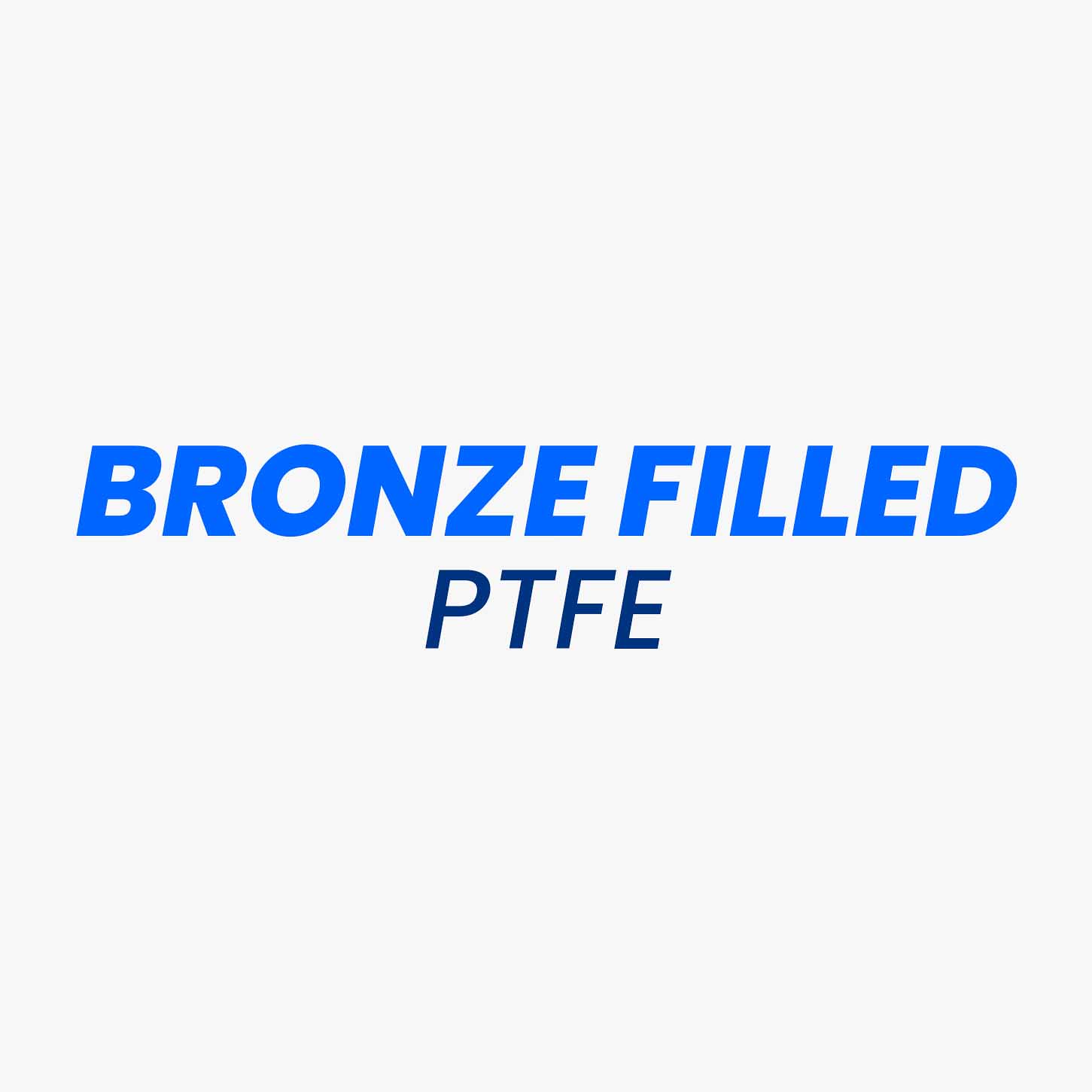
BRONZE FILLED PTFE
PRODUCT DESCRIPTION:
Bronze powder is used as a filler for reinforcing the Bronze filled PTFE. According to the application requirement, the filler percentage composition of the bronze powder can be accommodated as per requirement. The Bronze filled PTFE products have excellent dimensional stability and their creep resistance, wear resistance and thermal conductivity properties are superior then glass-filled PTFE products. The products using this material grade can be produced by using Ram extrusion, Isostatic and Compression moulding manufacturing methods. Bronze filled PTFE components are suitable for applications where a part is subjected to thermo-mechanical loads.
PROPERTIES:
- High specific gravity
- Excellent compressive strength
- Excellent temperature resistance
- Excellent wear resistance
- Low permeability
- Improved hardness
- High abrasion resistance
- Low coefficient of friction
APPLICATIONS:
Bronze filled PTFE has a wide range of applications. They are:
- Piston rings
- Bearing rings
- Valve seats
- Guideways
- High performance seals
- Compressor Industry
- Automotive Industry
Bronze powder is used as a filler for reinforcing the Bronze filled PTFE. According to the application requirement, the filler percentage composition of the bronze powder can be accommodated as per requirement. The Bronze filled PTFE products have excellent dimensional stability and their creep resistance, wear resistance and thermal conductivity properties are superior then glass-filled PTFE products. The products using this material grade can be produced by using Ram extrusion, Isostatic and Compression moulding manufacturing methods. Bronze filled PTFE components are suitable for applications where a part is subjected to thermo-mechanical loads.
PROPERTIES:
- High specific gravity
- Excellent compressive strength
- Excellent temperature resistance
- Excellent wear resistance
- Low permeability
- Improved hardness
- High abrasion resistance
- Low coefficient of friction
APPLICATIONS:
Bronze filled PTFE has a wide range of applications. They are:
- Piston rings
- Bearing rings
- Valve seats
- Guideways
- High performance seals
- Compressor Industry
- Automotive Industry

BRONZE-MOLY FILLED PTFE
PRODUCT DESCRIPTION:
Moly (or Molybdenum Disulfide, MoS2) incorporates a lubricating effect, hence when added provides excellent anti-friction property to the product. Whereas, the Bronze-filled PTFE products do have excellent creep resistance, wear resistance and heat conductivity properties. But it has a higher resistance to friction as compared to other filled PTFE grades. Therefore, by using moly and bronze as additives in PTFE, the starting coefficient of friction is reduced, as well as enhancing the thermal conductivity, creep, and wear resistance properties. The Bronze-moly filled PTFE components have higher resistance to pressure and lower seals abrasion characteristics. Bronze-moly filled PTFE is available in any ratio required.
PROPERTIES:
-High creep resistance
- Excellent compressive strength
- Excellent temperature resistance
- Excellent wear resistance
- Low permeability
- Low moisture absorption
- Improved hardness
- High abrasion resistance
- High tensile strength
- Low coefficient of friction
APPLICATIONS:
Bronze-moly filled PTFE has a wide range of applications. They are:
- Bushings
- Bearings
- Hydraulic high-performance seals
- Piston rings
- Bearing rings
- Valve seats
- Guideways
- Extrusion rings
- Compressor Industry
- Automotive Industry
Moly (or Molybdenum Disulfide, MoS2) incorporates a lubricating effect, hence when added provides excellent anti-friction property to the product. Whereas, the Bronze-filled PTFE products do have excellent creep resistance, wear resistance and heat conductivity properties. But it has a higher resistance to friction as compared to other filled PTFE grades. Therefore, by using moly and bronze as additives in PTFE, the starting coefficient of friction is reduced, as well as enhancing the thermal conductivity, creep, and wear resistance properties. The Bronze-moly filled PTFE components have higher resistance to pressure and lower seals abrasion characteristics. Bronze-moly filled PTFE is available in any ratio required.
PROPERTIES:
-High creep resistance
- Excellent compressive strength
- Excellent temperature resistance
- Excellent wear resistance
- Low permeability
- Low moisture absorption
- Improved hardness
- High abrasion resistance
- High tensile strength
- Low coefficient of friction
APPLICATIONS:
Bronze-moly filled PTFE has a wide range of applications. They are:
- Bushings
- Bearings
- Hydraulic high-performance seals
- Piston rings
- Bearing rings
- Valve seats
- Guideways
- Extrusion rings
- Compressor Industry
- Automotive Industry

PIGMENTED PTFE
PRODUCT DESCRIPTION:
The Pigmented PTFE material consists of a dry pigment along with other fillers. The addition of pigments can improve wear and compressive properties as compared to normal compounds. Pigmented PTFE products can be used in applications where color coding is required for part identification. This helps in reduce errors during assembly or servicing, where similar PTFE parts are present. The Pigmented PTFE components are mostly used because of their non-abrasive property.
PROPERTIES:
- Improved mould flow properties
- Non-abrasiveness
- Excellent compressive strength
- Good thermal conductivity
- Excellent wear resistance
- Excellent chemical resistance
- Low permeability
- Low coefficient of friction
- Flame-retardant properties
- Excellent dielectric properties
APPLICATIONS:
Pigmented PTFE has a wide range of applications. They are:
- Nozzles
- PTFE flanges
- PTFE plates
- PTFE chemical trays
- PTFE packing
- Piston rings
- Gaskets
- Electrical connectors
- Chemical & Pharmaceutical Industry
- Automotive Industry
- Food and Medical Industry
- Packaging industry
The Pigmented PTFE material consists of a dry pigment along with other fillers. The addition of pigments can improve wear and compressive properties as compared to normal compounds. Pigmented PTFE products can be used in applications where color coding is required for part identification. This helps in reduce errors during assembly or servicing, where similar PTFE parts are present. The Pigmented PTFE components are mostly used because of their non-abrasive property.
PROPERTIES:
- Improved mould flow properties
- Non-abrasiveness
- Excellent compressive strength
- Good thermal conductivity
- Excellent wear resistance
- Excellent chemical resistance
- Low permeability
- Low coefficient of friction
- Flame-retardant properties
- Excellent dielectric properties
APPLICATIONS:
Pigmented PTFE has a wide range of applications. They are:
- Nozzles
- PTFE flanges
- PTFE plates
- PTFE chemical trays
- PTFE packing
- Piston rings
- Gaskets
- Electrical connectors
- Chemical & Pharmaceutical Industry
- Automotive Industry
- Food and Medical Industry
- Packaging industry

PEEK
PRODUCT DESCRIPTION:
As the demand for products with reduced weight, higher strength, and durability is growing, the traditional metals can be replaced, by using PEEK (Polyether ether ketone) as an alternate solution. PEEK is a semi-crystalline thermoplastic material, which has excellent mechanical and thermal characteristics along with high chemical and wear resistance.
We also provide PEEK filled PTFE grade products, that showcase excellent sliding or low friction and higher wear resistance properties. This product has common applications in the food industry, because of its unique mechanical, chemical, and thermal properties.
PROPERTIES:
- Improved mould flow properties
- Excellent compressive strength
- Good thermal conductivity
- Excellent wear resistance
- Excellent creep resistance
- Excellent chemical resistance
- Low coefficient of friction
- Flame-retardant properties
- Excellent dielectric properties
APPLICATIONS:
PEEK has a wide range of applications. They are:
- Bearing cages
- Ball valve seats
- Piston rings
- Gaskets
- Seals
- Electrical insulators
- Chemical & Pharmaceutical Industry
- Automotive Industry
- Food and Medical Industry
- Oil and Gas Industry
As the demand for products with reduced weight, higher strength, and durability is growing, the traditional metals can be replaced, by using PEEK (Polyether ether ketone) as an alternate solution. PEEK is a semi-crystalline thermoplastic material, which has excellent mechanical and thermal characteristics along with high chemical and wear resistance.
We also provide PEEK filled PTFE grade products, that showcase excellent sliding or low friction and higher wear resistance properties. This product has common applications in the food industry, because of its unique mechanical, chemical, and thermal properties.
PROPERTIES:
- Improved mould flow properties
- Excellent compressive strength
- Good thermal conductivity
- Excellent wear resistance
- Excellent creep resistance
- Excellent chemical resistance
- Low coefficient of friction
- Flame-retardant properties
- Excellent dielectric properties
APPLICATIONS:
PEEK has a wide range of applications. They are:
- Bearing cages
- Ball valve seats
- Piston rings
- Gaskets
- Seals
- Electrical insulators
- Chemical & Pharmaceutical Industry
- Automotive Industry
- Food and Medical Industry
- Oil and Gas Industry
bottom of page